Designing a 500L Hop Extraction Tank for Craft Breweries
- Apr 27, 2025
- 168
- tiantai
At Tiantai Brewtech, we understand that efficient hop extraction is essential for producing exceptional craft beer. Based on our experience designing hop extraction systems for breweries around the world, we would like to share an overview of how we engineered a 500L Hop Extraction Tank, highlighting key design features and considerations that help brewers achieve the best aroma and flavour results.
Overview of the 500L Hop Extraction Tank
Our 500L Hop Extraction Tank is designed to optimise hop oil and aroma extraction through careful control of agitation, flow, and temperature.
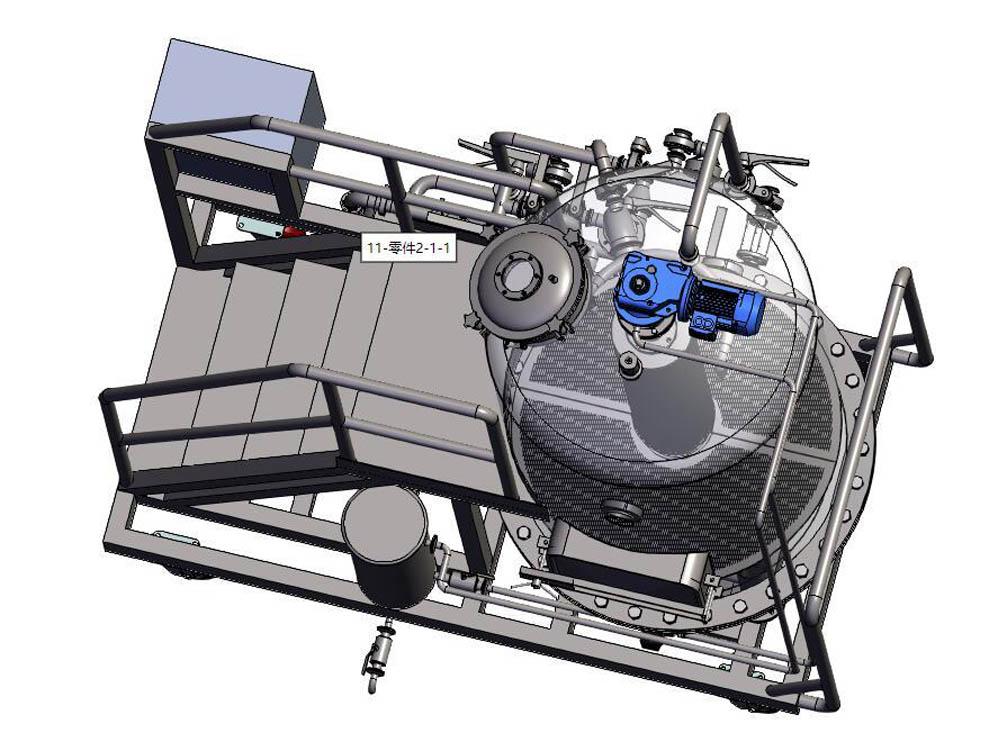
Key features of our design include:

Key Design Considerations
1. Purpose and Process
Objective: To extract essential hop oils, alpha acids, and volatile aromas during dry hopping or whirlpool hopping stages.
Extraction Methods: The system uses mechanical agitation, continuous recirculation, and optional gas sparging (CO₂ or N₂) to maximise extraction efficiency.
2. Material and Construction
Material: Constructed from food-grade stainless steel (SS304/SS316) for corrosion resistance and long service life.
Wall Thickness: 3–5 mm to ensure durability and withstand pressure fluctuations.
Internal Finish: Mirror-polished to reduce hop particle adhesion and simplify cleaning.
3. Tank Configuration
Capacity: Nominal 500L working volume with 10–20% headspace to accommodate foaming during agitation.
Shape: Cylindrical body with a 30°–45° conical bottom to facilitate easy hop removal.
Top Access: Dome-shaped top with a sanitary manway for hop addition and internal access.
4. Agitation and Extraction
Rotating Screen Agitator: Provides consistent hop dispersion throughout the liquid.
Optional Gas Sparging Arm: Allows CO₂ or nitrogen injection at the tank base to create additional turbulence and enhance extraction.
5. Flow and Filtration
Inlet: Side or tangential inlet designed for even saturation of hops.
Outlet: Bottom outlet fitted with a fine mesh or filter screen to separate hop solids from the beer.
Valves: Sanitary tri-clamp butterfly valves for easy operation and cleaning.
Sight Glass: Allows brewers to visually monitor extraction progress and flow.
6. Pressure and Temperature Management
Pressure Rating: Built to safely handle up to 2 bar operating pressure.
Cooling Jacket (Optional): A glycol jacket can be added to maintain temperature during extraction, preventing unwanted isomerization of hop compounds.
7. Cleaning and Maintenance
CIP Ready: Equipped with a spray ball or rotary spray head for effective cleaning in place (CIP).
Full-Drain Design: Sloped bottom and strategic outlet positioning eliminate dead zones and ensure complete hop removal.
8. Automation and Monitoring (Optional)
Control Panel: Offers real-time monitoring of temperature, pressure, and recirculation rates.
Sensor Integration: Optional temperature and pressure sensors for greater process control and automation.
9. Space-Saving Modular Design
The skid-mounted structure is designed with space efficiency in mind, with the option for modular assembly to accommodate transport or installation through restricted spaces such as freight elevators.
Conclusion
The 500L Hop Extraction Tank from Tiantai Brewtech is engineered to provide brewers with maximum extraction efficiency, operational reliability, and flexibility.
Whether you are expanding your craft brewery or upgrading your hop utilisation processes, our custom-designed solutions are ready to support your brewing excellence.
Interested in learning more?
Contact Tiantai Brewtech today to discuss your brewery’s needs and get a customised solution for your hop extraction system.
Edited by Nicole
Sales manager | Tiantai brewtech
Email: [email protected]
Overview of the 500L Hop Extraction Tank
Our 500L Hop Extraction Tank is designed to optimise hop oil and aroma extraction through careful control of agitation, flow, and temperature.
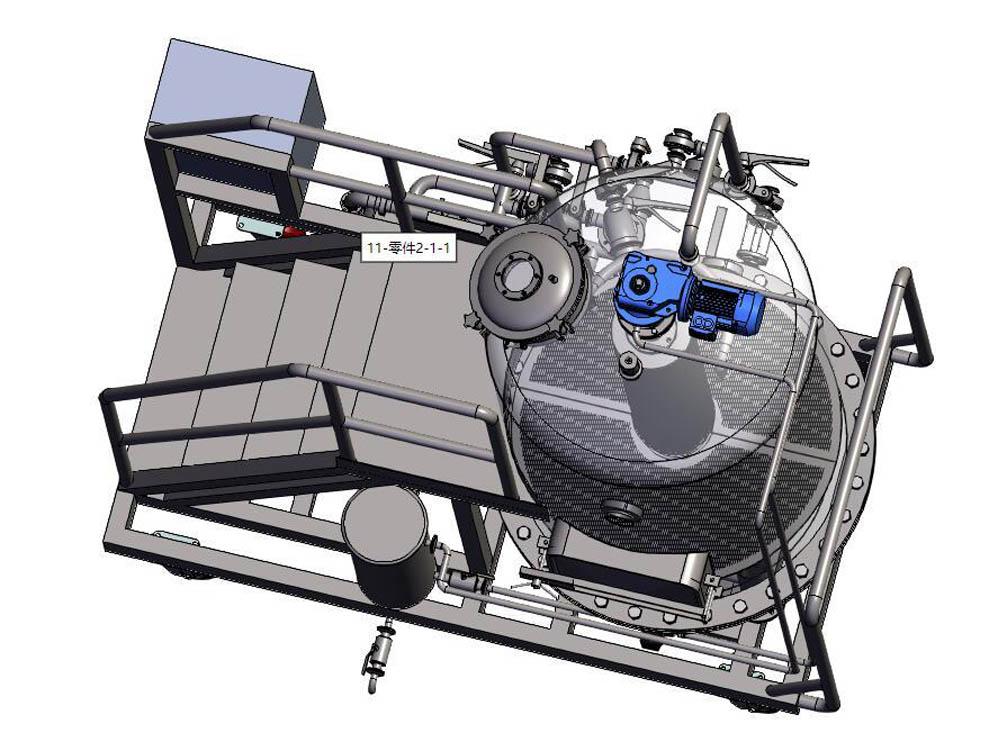
Key features of our design include:
- Top-Mounted Mixer Motor: A motor drives an internal rotating filter screen to ensure thorough mixing of beer and hops, enhancing extraction efficiency.
- Motor Cooling System: To prevent overheating during continuous operation, a dedicated cold water tank is integrated to cool the motor.
- Skid-Mounted Design with Platform: The complete system, including the diaphragm pump, is mounted on a skid for easy mobility. A custom platform is included to ensure comfortable and safe operation given the tank's height.

Key Design Considerations
1. Purpose and Process
Objective: To extract essential hop oils, alpha acids, and volatile aromas during dry hopping or whirlpool hopping stages.
Extraction Methods: The system uses mechanical agitation, continuous recirculation, and optional gas sparging (CO₂ or N₂) to maximise extraction efficiency.
2. Material and Construction
Material: Constructed from food-grade stainless steel (SS304/SS316) for corrosion resistance and long service life.
Wall Thickness: 3–5 mm to ensure durability and withstand pressure fluctuations.
Internal Finish: Mirror-polished to reduce hop particle adhesion and simplify cleaning.
3. Tank Configuration
Capacity: Nominal 500L working volume with 10–20% headspace to accommodate foaming during agitation.
Shape: Cylindrical body with a 30°–45° conical bottom to facilitate easy hop removal.
Top Access: Dome-shaped top with a sanitary manway for hop addition and internal access.
4. Agitation and Extraction
Rotating Screen Agitator: Provides consistent hop dispersion throughout the liquid.
Optional Gas Sparging Arm: Allows CO₂ or nitrogen injection at the tank base to create additional turbulence and enhance extraction.
5. Flow and Filtration
Inlet: Side or tangential inlet designed for even saturation of hops.
Outlet: Bottom outlet fitted with a fine mesh or filter screen to separate hop solids from the beer.
Valves: Sanitary tri-clamp butterfly valves for easy operation and cleaning.
Sight Glass: Allows brewers to visually monitor extraction progress and flow.
6. Pressure and Temperature Management
Pressure Rating: Built to safely handle up to 2 bar operating pressure.
Cooling Jacket (Optional): A glycol jacket can be added to maintain temperature during extraction, preventing unwanted isomerization of hop compounds.
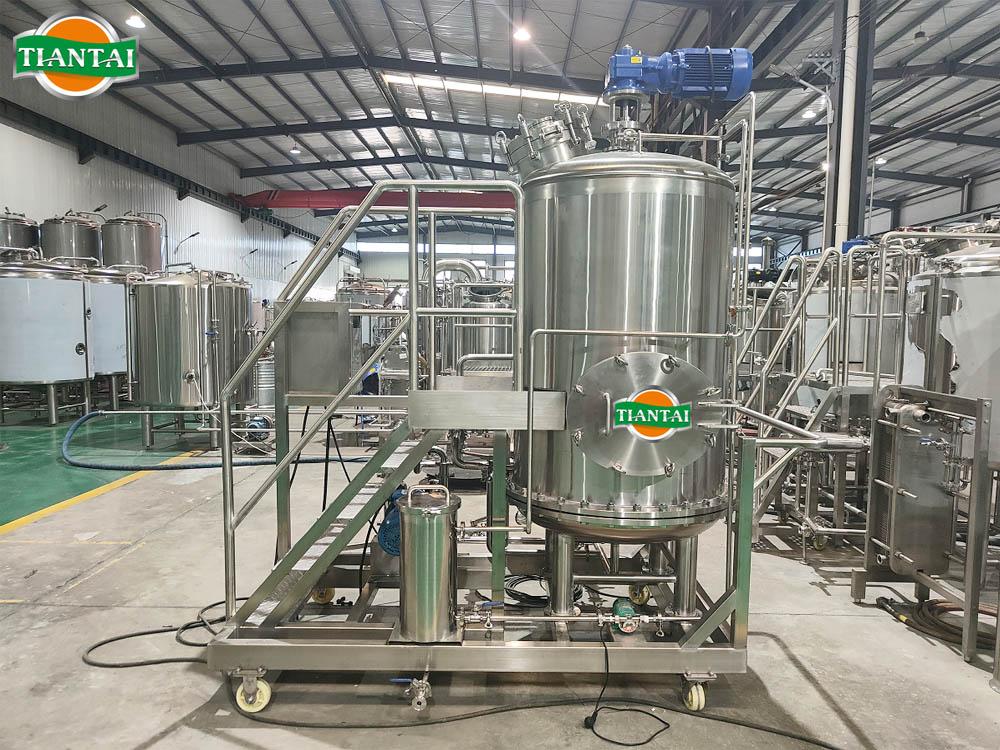
7. Cleaning and Maintenance
CIP Ready: Equipped with a spray ball or rotary spray head for effective cleaning in place (CIP).
Full-Drain Design: Sloped bottom and strategic outlet positioning eliminate dead zones and ensure complete hop removal.
8. Automation and Monitoring (Optional)
Control Panel: Offers real-time monitoring of temperature, pressure, and recirculation rates.
Sensor Integration: Optional temperature and pressure sensors for greater process control and automation.
9. Space-Saving Modular Design
The skid-mounted structure is designed with space efficiency in mind, with the option for modular assembly to accommodate transport or installation through restricted spaces such as freight elevators.
Conclusion
The 500L Hop Extraction Tank from Tiantai Brewtech is engineered to provide brewers with maximum extraction efficiency, operational reliability, and flexibility.
Whether you are expanding your craft brewery or upgrading your hop utilisation processes, our custom-designed solutions are ready to support your brewing excellence.
Interested in learning more?
Contact Tiantai Brewtech today to discuss your brewery’s needs and get a customised solution for your hop extraction system.
Edited by Nicole
Sales manager | Tiantai brewtech
Email: [email protected]